Foundry’s waste heat used for heating paintshops
19/05/2025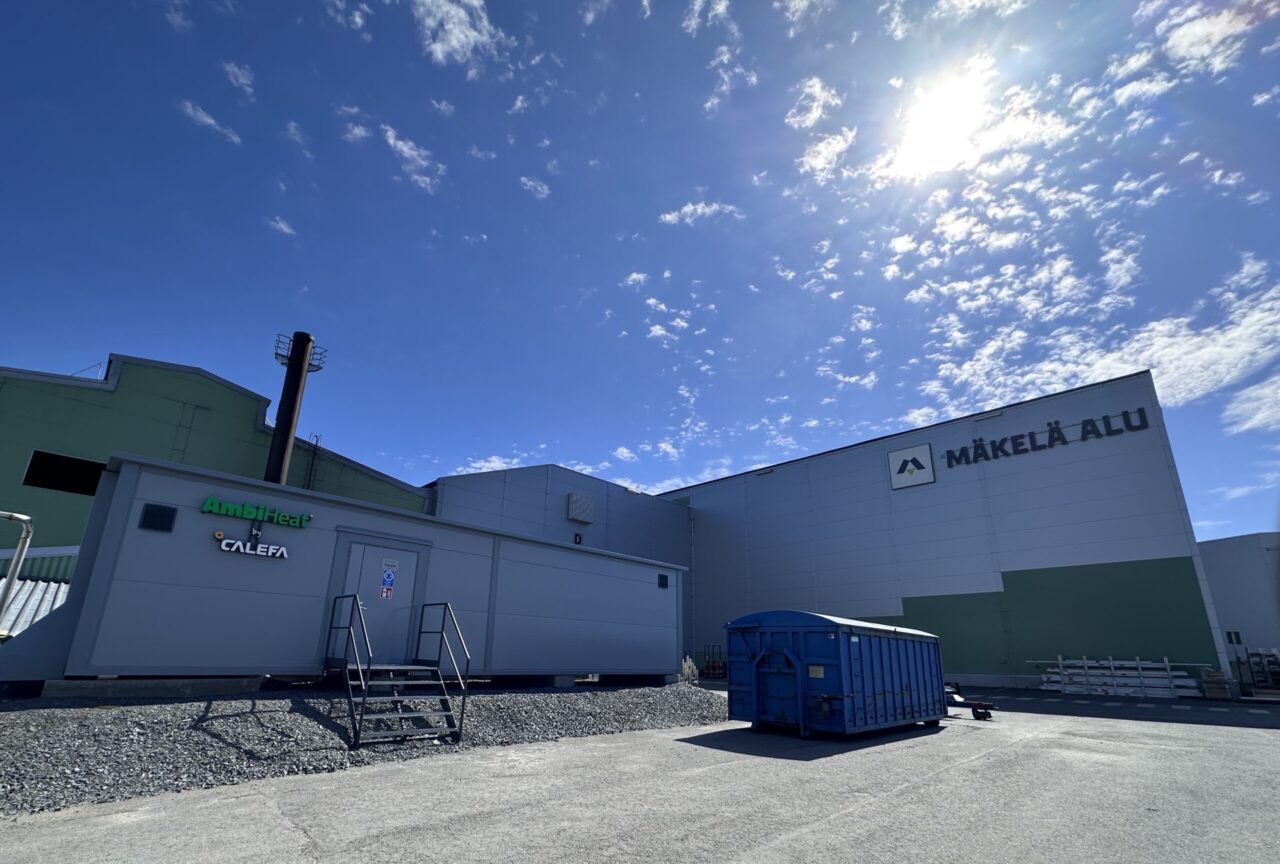
We have implemented new heat pump technology to recover waste heat from the foundry at our Luoma-aho plant. The recovered heat is used to warm up the paintshops.
– The heat recovery and pump system replaces the use of liquefied gas in the pre-treatment processes of both coating lines. The waste heat is collected from the foundry’s cooling water basin. This water is generated when castings are cooled with water, explains Tomi Pilbacka, Development Manager.
The foundry produces Mäkelä Alu’s own recycled billet by casting recycled aluminium. The idea of capturing heat from the cooling water originated nearly ten years ago.
– Together with the equipment supplier, we explored different possibilities for utilising process waste heat, and this was identified as one of the most promising targets, says Reijo Seppälä, Project Manager.
The system replaces liquefied gas
With the new system in place, the thermal energy recovered from the foundry is used to heat the pre-treatment water in both coating lines and the horizontal coating line. Before powder coating, the aluminium profiles are washed – previously, this process water was heated with liquefied gas.
– Once the new system is fully operational, we’ll be able to eliminate the use of liquefied gas in these heating needs, Pilbacka states.
Since cooling water is only generated when casting is in progress, the system includes an electric backup boiler that operates with clean electricity.
Container solution allows mobility
The equipment was installed in a separate container that was preassembled at the factory. On site, piping and electrical work was carried out by local contractors.
– This solution is cost-efficient and, if needed, movable. Commissioning is still ongoing, but the system will be fully up and running shortly, Seppälä says.
The equipment supplier was the Finnish company Calefa, specialised in heat pump solutions, and the project was also carried out in cooperation with local piping and electrical companies.
The solution will result in a reduction of 290 tonnes of CO₂ emissions already this year. The investment is valued at approximately €360,000 and will bring substantial energy savings by eliminating liquefied gas usage.
The foundry heat recovery project is part of a larger investment programme aimed at reducing CO₂ emissions from our own production. The project received energy investment support (RRF) from the Ministry of Economic Affairs and Employment of Finland.