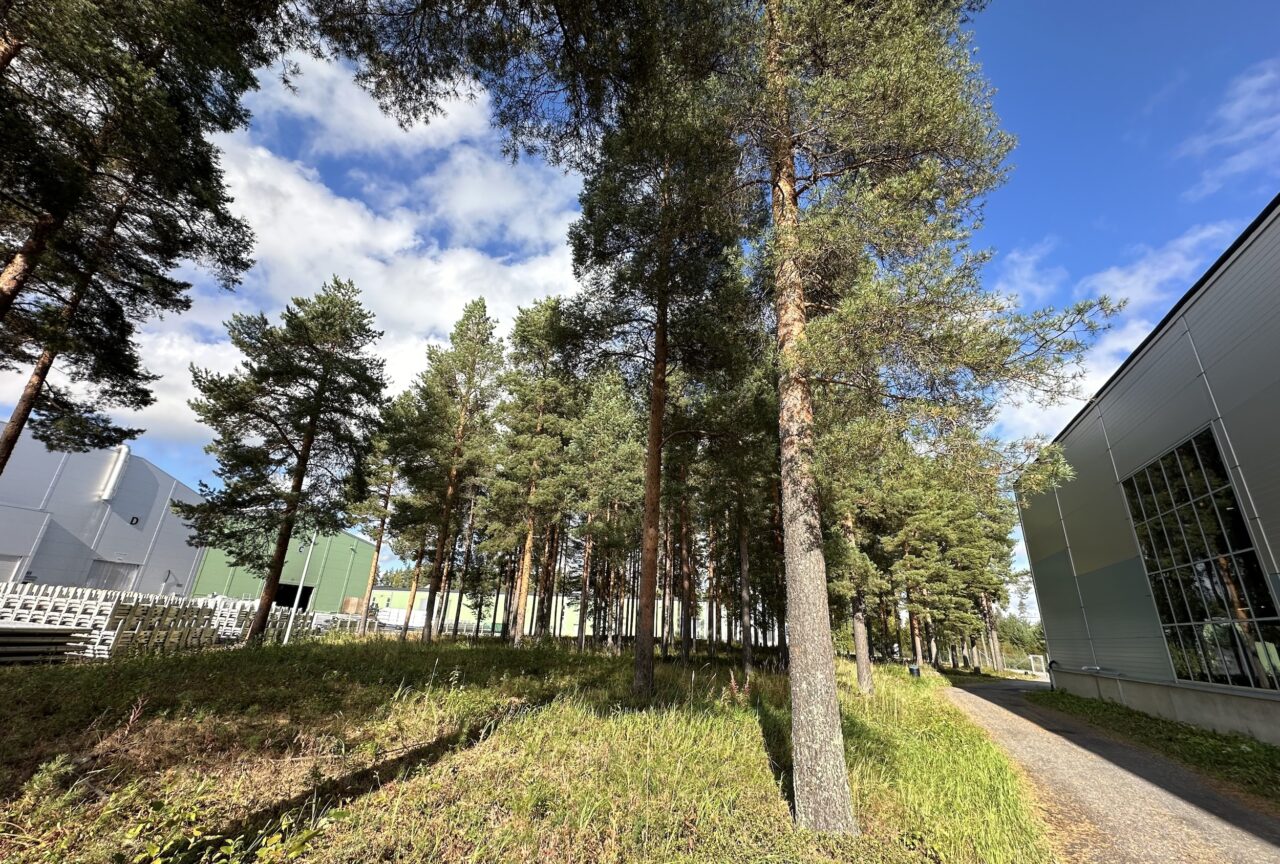
Our goal is to keep emissions into the air, soil and water as low as possible. Some emissions inevitably occur, so our activities are subject to an environmental permit. This article outlines some examples of what we measure to meet our goals and comply with relevant regulations.
Our emissions limit values are set by an environmental permit granted by the Regional State Administrative Agency.
“An environmental impact assessment was carried out for the permit. The assessment also took into account the expansion of activities and increase in capacity. Of course, as our capacity increases, we use more energy, raw materials, and water,” says Päivi Venesoja, EHSQ Manager.
Emissions are reported on a regular basis
Environmental permits require quarterly monitoring and reporting of all emissions.
“Once a quarter, we report certain parameters of the water entering and leaving our wastewater treatment plant, among other things. These parameters include chemical oxygen demand, the concentration of solids, phosphorus, nickel and aluminium, and pH values. Reporting is made to the ELY Centre, which is the supervisory environmental authority,” says Päivi Venesoja.
The data are obtained from a wastewater analysis carried out by an external operator. Analysis samples are taken by an automatic collector once a month. Samples are collected for 24 hours so that the obtained value is as realistic as possible.
A wider range of emissions are reported annually.
“Although there is no reporting obligation, we monitor things like the amount of waste powder coating per coated metre, CO2 emissions from our gate to the customer’s gate, and the amount of reclaimed waste recovered from the total amount of waste during a certain period,” continues Päivi.
Wastewater treatment
The wastewater treatment plant process is very efficient, and its operation is continuously monitored by automatic operating monitoring systems.
“As far as wastewater is concerned, we have nothing to worry about because we are well below the limit values. For example, the amount of solids per litre should not exceed 50 milligrams, and last year we had an average of 20 milligrams,” says Päivi Venesoja.
The purified wastewater that meets the limit values is eventually discharged into the nearby Mikinpuro stream.
The final analysis is carried out on the water system.
“We have five water system observation points where an external operator collects samples. There are lots of observation points, not just ours. Over the past 15 years, there have been no major fluctuations in the samples or any other alarming findings,” says Päivi.
Less frequent reporting in Voikkaa
The activities of our Voikkaa plant are not subject to an environmental permit. However, the plant does use materials such as solvents.
“We have therefore had to register our activities in the environmental protection information system. We annually report water and energy consumption plus solvent quantities to the local ELY Centre. The wastewater from our Voikkaa plant is channelled to the Kuusankoski business cluster for joint wastewater treatment. However, we are interested in our own activities, so we regularly carry out a comprehensive analysis of our wastewater. The analysis is compared to the previous year’s data,” says Päivi.
Emissions into the air
Emissions into the air are monitored at our anodizing plant, powder-coating paint shops, extrusion lines, and foundry.
“We measure all consumption: the use of liquefied gas and fuel, carbon dioxide and particulate emissions, nitrogen oxides and hydrochloric acid, while ammonia, nickel compounds and cobalt are also monitored in the anodizing process. We use the latest air emission measurement equipment to find values such as how many milligrams of a heavy metal or hydrochloric acid are released into the air per hour,” says Päivi Venesoja.
The measured values are used to calculate average hourly emissions, and these are compared with figures from previous years.
“Emissions can be reduced by using newer technology. For example, renewing the energy system at our anodizing plant has significantly contributed to the reduction of carbon dioxide and particulate emissions,” she continues.
Mäkelä Alu is also part of the Seinäjoki region’s bioindicator research, in which we voluntarily participate by covering the costs of a measurement point.
“We have also signed an energy efficiency agreement. By participating in the agreement, we are committing ourselves to increasing energy efficiency in all our activities. The agreement also obliges us to report all energy consumption and measures to reduce energy consumption.”
Emissions into the soil
Over the course of the year, we produce a total of about 2,000 tonnes of different waste. A significant part of this waste is reused. Only 1.75% of total waste was sent to landfill in 2023.
“Different forms of waste can be converted into energy, and this is what it is usually used for. Getting rid of hazardous or otherwise difficult to dispose of waste is expensive. We have therefore carried out investigations, surveys and experiments on how to utilise waste that is difficult to dispose of. Our efforts have resulted in some test projects on things like the utilisation of sediment and spent lye resulting from wastewater treatment,” says Päivi.
Carbon dioxide emissions continue to decrease
We have been carrying out our own emissions calculations since 2005. We have been able to reduce our carbon dioxide emissions by 51%, even though our operations have increased.
“Our calculations cover all forms of energy: electricity, liquefied and natural gases, all transport by contract carriers, transport within the factory area, and our own forklifts. These are calculated in tonnes produced per quarter,” says Päivi Venesoja.
“We have once again calculated emissions this year as we switched to zero-emission electricity at Voikkaa. All our forklifts have been replaced with biodiesel-powered forklifts this year. However, along with the renewal of the energy system at our anodizing plant, the heat recovery system installed in Voikkaa this year has also had a major impact on the current year’s emission reductions,” she continues.