The AluStorage® service meets the changing weekly needs
06/06/2021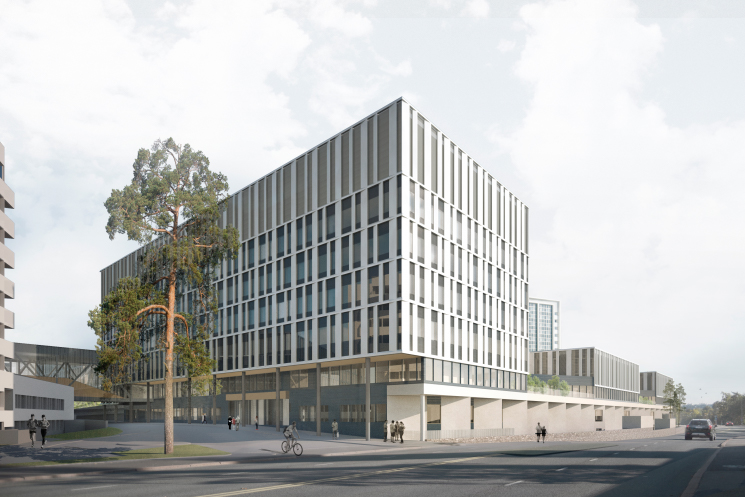
The Siltasairaala hospital in Helsinki is one of Alavus Ikkunat Oy’s customer sites in 2021. The company has delivered more than 1,000 external windows to the hospital. The hospital has ordered 1,100 interior windows, and they are currently being delivered.
Alavus Ikkunat Oy is one of largest window and door manufacturers in Finland. The company delivers approximately 60,000 windows and 10,000 doors a year. The company’s customers are mainly construction companies, housing companies, and nationwide retailers. The company delivers windows and doors for apartment buildings, hospitals, schools, and other public buildings.
Every week in production is different, but one thing never changes: construction sites need their products on time, so it’s important for raw materials to be in production on time.
“Otherwise, we have 60–70 people twiddling their thumbs, and at the same time our customers’ construction site stands idle,” says Plant Manager Juha Äijänaho.
“However, we have not yet experienced such a situation, thanks to our reliable partners. Mäkelä Alu is one of our longest-serving partners. They have supplied us with aluminium profiles for almost 20 years.”
Reliable delivery and guaranteed quality
Mäkelä Alu delivers aluminium profiles to the Alavus Ikkunat factory once or twice a week: always according to the customer’s needs.
“In addition to reliable delivery, we can rely on the quality of the profiles. That is important to us, because we want to provide the highest level of quality to our customers as well,” says Äijänaho.
Alavus Ikkunat needs aluminium profiles for its window frames and the cladding of balcony doors, among other things.
The company delivers a variety of special windows for its customers’ construction projects.
The AluStorage® service frees up capital from warehousing
With Mäkelä Alu’s AluStorage® service, which has been developed based on customer needs, production can be planned on a weekly basis without having to invest money or space in a warehouse.
Mäkelä Alu supplies approximately 20 different profile models to Alavus Ikkunat. All of them are always ready in Mäkelä Alu’s warehouse. New aluminium profiles are made as the stock levels start to dwindle.
“The aluminium profiles are delivered to us according to order. We do not have our own warehouse. We place the orders electronically,” says Äijänaho.
Alavus Ikkunat utilises Mäkelä Alu’s additional services when designing new aluminium profile models. Mäkelä Alu can create 3D models of the profiles, if necessary.
“A profile printed from plastic makes it easy to test the functionality of the model before the extrusion of the new profiles.”
Mäkelä Alu’s warehouse guarantees fast deliveries
When the customer places an order, Mäkelä Alu takes care of coating the agreed aluminium profiles. Special paints are purchased to order.
“If necessary, the aluminium profiles can be delivered as soon as the following week,” says Mäkelä Alu’s Sales Manager Asko Perälampi.
Although the aluminium profiles are made according to the customer’s drawings, the customer only pays for the profiles when they use them.
“Some aluminium profiles have a faster storage cycle. Others are needed less frequently and may sit in our warehouse for several months,” says Perälampi.
The profiles are generally delivered to the customer in a length of six metres. The customer cuts the profiles to their final length and performs the necessary machining.
Mäkelä Alu caters for all colour needs
The design and colour needs of Alavus Ikkunat change every week. Today, windows and doors can be coated in a wide range of colours.
“Of course, the majority of the profiles we order are made in standard colours, such as white or dark grey. However, our customers use a variety of colours in their construction projects. Especially in public spaces, architects use colours boldly: red, yellow, blue…even the brightest shades. Even I am amazed at times,” says Äijänaho.
Fortunately, the world has plenty of room for colours, and so does Mäkelä Alu’s powder-coating paint shop.
AluBasket® delivers aluminium profiles neatly and conveniently
The profiles are delivered to Alavus in Mäkelä Alu’s light aluminium baskets, which make the profiles easy to handle both during transport and at the factory. The AluBasket® service is designed to facilitate the transport, handling and temporary storage of long aluminium profiles.
“The baskets protect the profiles from dents and scratches. This is particularly important when the profiles are intended for windows and doors, i.e., visible elements. The baskets keep the profiles straight, which is also important, because we have to be able to get the panes and seals into the profile gaps,” says Äijänaho.
The profiles can also be sorted in different baskets.
“The baskets make the profiles easy to handle with a forklift in our factory.
The baskets are light, so they can be moved single-handedly.”
The AluBasket® service reduces the amount of packaging material
The baskets help keep the profiles in good order. They can also be used to move extra profiles off the production line.
“It’s a clear advantage over cable-tying the profiles together and delivering them on a pallet. Moving a pile like that is not quite as easy,” says Perälampi.
The empty baskets can be stacked, so they require little storage space. The AluBasket® service also includes the possibility of storing the profiles at the customer’s premises for a slightly longer period of time.
“The aluminium profiles we order are always used so quickly that the circulation time of the baskets is only a few weeks,” says Äijänaho.
One advantage of the service is that the baskets can be circulated, which significantly reduces the amount of packaging material. The use of the AluBasket® service is separately agreed upon ordering.
Sometimes it’s good to meet face to face
According to Äijänaho, cooperation with Mäkelä Alu has always been smooth. There have been very few complaints.
“Even in such cases, everything is handled very well,” says Äijänaho in praise of Mäkelä Alu.
Carefully planned services make operations run smoothly. However, with highly automated services, face-to-face contact with people remains fairly limited. This has also been taken into account.
“We tend to visit Mäkelä Alu every few years, and their representatives visit us every year. That is important. Sometimes it’s good to meet face to face and talk about something other than aluminium,” says Äijänaho.
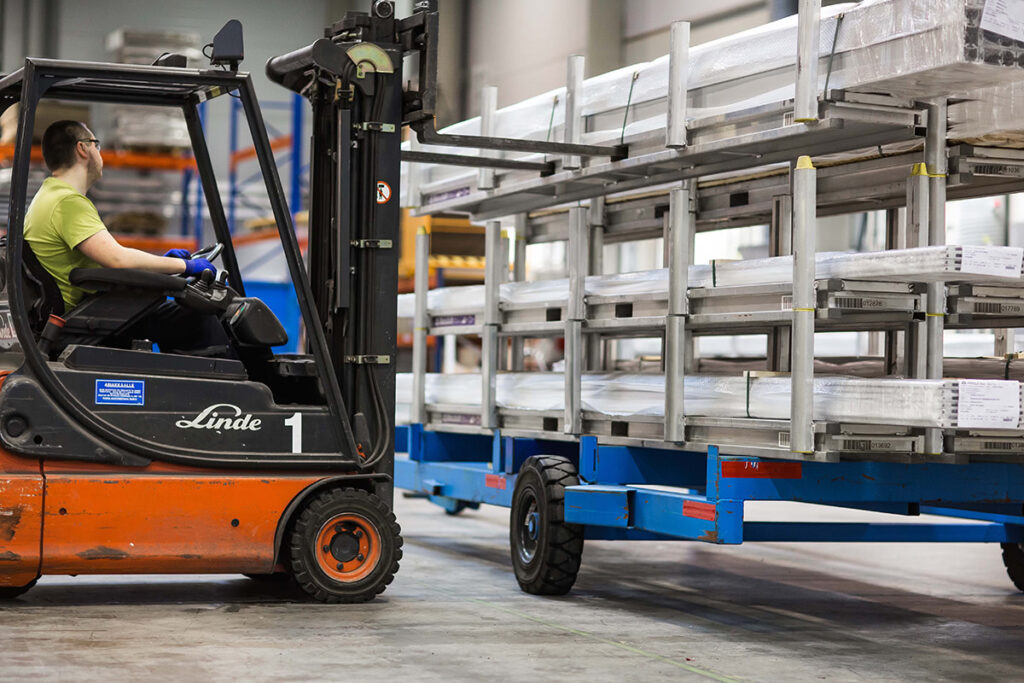
AluBasket® baskets facilitate the transport, storage and transfer of aluminium profiles.