Responsible and environmentally friendly aluminium profile production
22/11/2023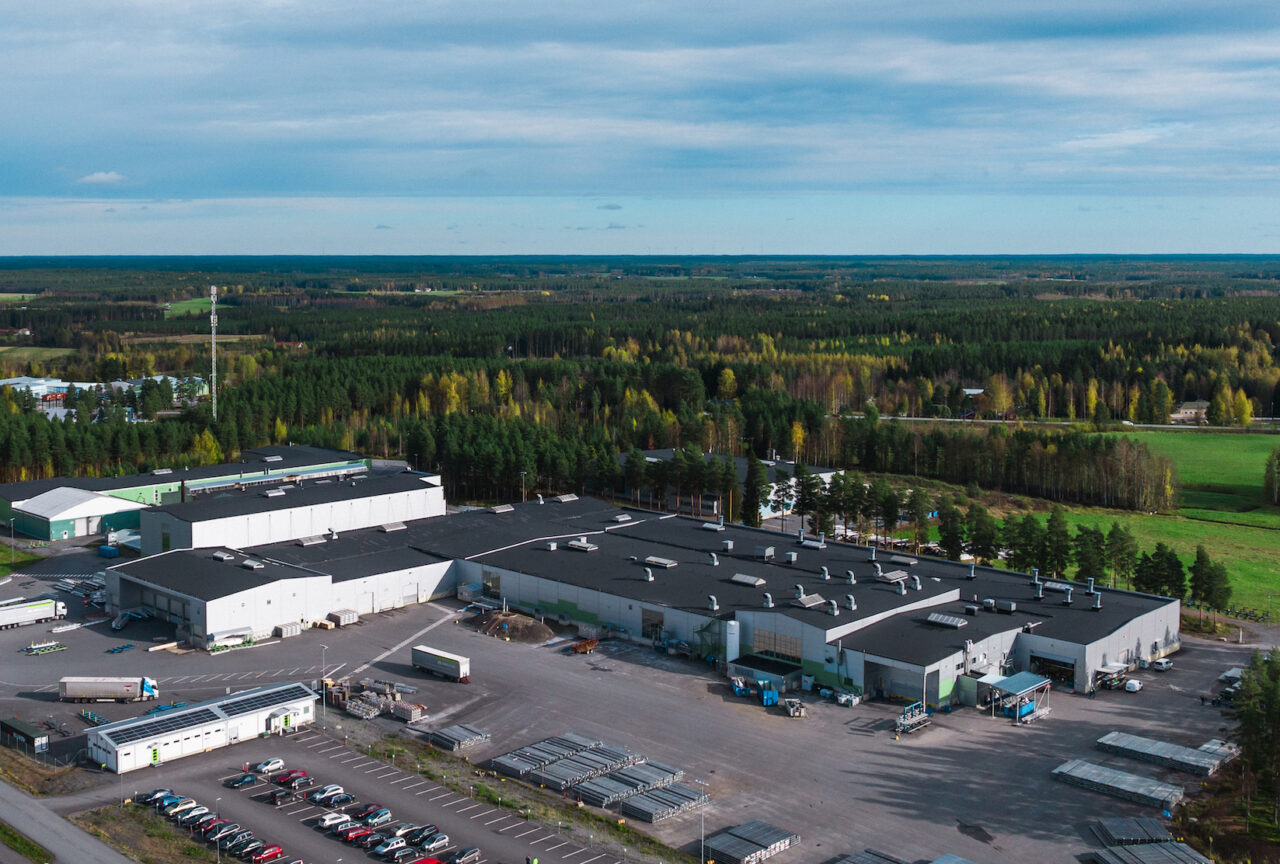
“This article has been published in the Nordische Profis 2023 publication.”
A responsible and modern aluminium extrusion plant nestled amongst Finnish forests – this is Mäkelä Alu. In this article, we explain what measures we have taken to be more energy-efficient and environmentally friendly. Our customers across Europe appreciate our services, which bring valuable cost benefits to their processes.
We have invested in sustainable production and environmentally friendly solutions for years. Our production will be completely carbon neutral by the end of 2025. To this end, we recently launched a development project worth approximately EUR 10 million to reduce emissions, increase energy efficiency, and combat climate change.
Phasing out LPG is a significant step
In the project, the most significant reduction in emissions will be achieved by replacing our LPG process heating appliances with electric ones. Electrification and the renewable energy sub-projects will require major changes to our factory’s internal electrical network.
“We will significantly reduce the use of LPG by electrifying production and increasing heat recovery. With these measures, we can reduce our carbon dioxide emissions by about 2,800 tonnes per year, which is about 40 per cent of our current emissions from production,” says Development Director Tomi Pilbacka.
LPG is currently used in applications such as billet heating on our two extrusion lines. These heating systems will be replaced by new technology that can use renewable electricity as energy. One of our three extrusion lines already uses electric billet heating.
“With heat recovery and heat pumps, we can eliminate the use of LPG, especially in our surface treatment lines and in the heating of buildings. In addition, we intend to build a 1 MWh electricity storage facility in the Alajärvi plant area,” Pilbacka continues.
Carbon-neutral anodizing will soon become a reality
This autumn, we can start talking about carbon-neutral anodizing, as we have completely renovated our anodizing plant’s energy system. The renovation was carried out in stages and the resulting system is completely unique; there is nothing exactly like it anywhere else in the world.
“In the first phase, we implemented a waste heat recovery solution with a heat pump system. Previously, the process was heated by a steam centre powered by LPG and cooled by electric coolers. First, we started utilising the heat generated in the anodizing tanks. With heat recovery, we were able to cool the tanks at the same time. With the above-mentioned solution, we were able to replace part of the heating produced by the steam centre with electricity,” Tomi Pilbacka explains.
In the second phase of the energy renovation, the heat pump system and heat recovery were expanded so that gas could be almost completely phased out from heat production.
“In addition to the heat pump, electric and gas boilers were also purchased. A gas-fired gas boiler is needed as a backup and as an additional source of heat in freezing weather, but otherwise all heating is produced by a heat pump and an electric boiler. The new gas boiler is also equipped to transition to using biogas. Our goal is to stop using LPG altogether,” he continues.
In anodizing, we also recover heat from wastewater. The plant’s heat recovery saves up to 1,800 megawatt-hours of energy per year.
Aluminium billets from recycled AluPure
More and more of our customers are monitoring the emissions and environmental impact of their production. Due to a new, environmentally conscious approach, interest in recycled aluminium has also increased. To respond to these needs, we offer our customers AluPure aluminium billets produced in our own foundry, which consist of 100% recycled aluminium. We have been producing recycled aluminium for a long time, as many of our customers look for the lowest possible primary percentage. Selecting aluminium profiles made from recycled aluminium billets allows you to reduce the carbon footprint of the final product.
The emissions of AluPure are very low, only 2.01 tn CO2e/t. The carbon dioxide equivalent (CO2e) describes the climate impact of human-produced greenhouse gases. The measurement unit used (tn CO2e/t) illustrates how many carbon dioxide equivalent tonnes are produced when a thousand kilogrammes of product are manufactured. By comparison, the average emissions of primary aluminium produced in Europe are 6.7 tn CO2e/t.
“The figures show that the choice of aluminium profile manufacturer can have a great impact on the climate and the environment. By choosing AluPure, you are making a choice for the environment and the climate,” says Päivi Venesoja, Mäkelä Alu’s EHSQ Manager.
Ecolabelled AluPure
Mäkelä Alu has completed an Environmental Product Declaration (EPD) for profiles made from both recycled AluPure and primary aluminium.
“An Environmental Product Declaration is a standardised, reliable way to present a life-cycle analysis of a product or service. An EPD is an independently verified and certified document that provides clear and comparable information about the environmental impact of a product throughout its life cycle,” says Päivi Venesoja.
AluPure also bears the Nordic Swan Ecolabel. Ympäristömerkintä Suomi Oy has approved the use of window profiles made from Mäkelä Alu’s recycled aluminium in Nordic Swan Ecolabelled buildings in accordance with the building requirement O25 (“Windows and outer doors of non-renewable materials”).
The label is an official ecolabel used in the Nordic countries, which means that the product or service meets the environmental criteria set for the label.
Quality partner for aluminium profile production
In addition to our environmental efforts, we also act responsibly by taking good care of our employees and being a reliable partner for our customers and suppliers. Mäkelä Alu’s AluServices® concept, a customer-oriented solution developed based on customer needs, aims to ensure that customers get the aluminium profiles they need as easily as possible and exactly when they need them.
The traditional method of buying large quantities of raw materials for storage as cheaply as possible ties up capital, takes up space, and hinders business growth and development. These are things that Mäkelä Alu’s customers do not have to worry about when purchasing aluminium profiles.
“This type of operating model does not meet current needs, and it does not allow us to respond to individual orders, especially those that contain profiles in customised colours,” says Mäkelä Alu’s Export Manager Janne Lager.
Our goal is not always to sell the product at the lowest price, but to offer the most cost-effective solution for the customer. After all, the final price is not solely determined by the price of raw materials, but by the efficiency of the entire production process.
“That is where our customised service packages bring added value. The overall benefits should be assessed by looking at the process as a whole, not just by focusing on the time of purchase,” says Lager.